Started building a RepRap
Project RepRap
I’ve started building a RepRap. Read more… Also take a look at the website: www.reprap.org
What is the RepRap
In short: It is a 3D printer capable of printing it’s own parts. Its operating principle is a computer controlled glue gun that can move in 3 directions (X, Y and Z). Z is the height coordinate and the RepRap ‘screws’ up/down a platform that is connected with 4 nuts, one on each corner. The X and Y are the horizontal carriages. Besides that it precisely controls the amount of plastic that the ‘glue gun’ extrudes (spits out). It’s not really glue, but thermoplasts (plastics that are deformable when hot, solid when they’ve cooled). The thermoplasts fuse together stream by stream to form a layer. The Z-platform is lowered a fraction with each layer. The picture on the right is an example of what it makes: it can print its own printing toolhead.
What is cool about the RepRap
Because of Self Replication, this project has to potential for exponential growth. If people print parts for a couple of their friends (a-la Pay it forward) they can use and improve RepRaps. Keep in mind that this is a first generation designed and built by a few people. RepRaps become better at a increasing speed as more people improve it, and there are more people that improve it because it’s user base extends at a growing rate. All users will be able to keep their system updated by downloading latest designs and printing those upgrades. If you were to model this as a System Dynamics model, there are several reinforcing loops.
Growth for the sake of growth?
Growth for the sake of growth is all too common. There have to be other benefits. There are 3 aspects that make this project worthwile:
- Learning. I think that everyone that has built a RepRap will have a more profound knowledge of mechanical construction, electronics and CAD /CAM (Computer Aided Design/Manufacturing). It is something that anyone can build, with a healthy dosis of persistence and experimentation.
- Creative products. The produce of the RepRap is only limited by your imagination… and that of others. If you find 3D models made by someone else you can (customize and) print those.
- Future RepRap generations. The power of the RepRap lies in its development. Over time, there will be modules such as recyclers (to reuse the plastic that you now throw away), 3D milling units, 3D scanners (so you can FAX, copy or digitize a physical object) and many other things. The fun part is that you can take part in this development. It could also make Open Source machines other than a RepRap.
I have no doubts that in the future, EVERYONE, will have a 3D printer in his home. One day, computers were for a few big corporations and institutes only. Right now most people cary more powerful devices around in the form of a phone, laptop, iPods, etc. The have become:
- Much cheaper
- Much more powerful
- Much smaller
- Less maintenance
- Widely adopted
The same, I believe will happen with the RepRap. It will handle more materials, be more robust, etc. And if this takes of, all this valuable intellectual property will be public domain. No one can own and restrict ownership or distribution it for personal profit. Many printable objects will become freely available just like free MP3s are more and more common.
Getting the goods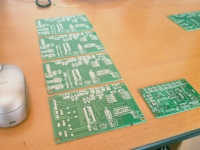
Electronic supplies took 2 days from the US based Mouser to the Netherlands. Also, Zach Smith was pretty fast with his shipment of PCBs (also 2 days after I knew he shipped it). Doing all the ordering via the BoM (Bill of Materials) tool reduced the ordering process to a few clicks. The shipment of plastic Moulded parts for the RepRap takes a little longer because Ian Adkin unfortunately (mostly for them of course) had an ill co-worker.
All together I expect to spend about 500 euros. This is higher than the 400 euro mark, because I also ordered all the parts that someone with a RepRap could make more cheaply.
Soldering it
Soldering the first board was very easy. All instructions are very detailed. If you have experience with electronics you have to be careful not to skip the explanations and just build it the way you think you’re supposed to. My advice (if you’re somewhat chaotic like me) is to follow the instructions step by step: they are well thought out and you’re almost certainly going to forget something somewhere…
Subsequent boards are simple as well. You need 5 controller boards (in the PIC based electronics variant, there is an alternative). 3 boards are for the X,Y and Z axis, 2 for the two extruders/toolheads that you can use. All boards are the same up to a certain point. At this point the X, Y and Z boards are finished as stepper controllers with a synchronization link between them, and the extruder controllers to make temperature measurements, regulate a heating coil, control a fan and to regulate extrusion speeds (a DC motor). Stepper motors are different from the well known DC motors. Look at wikipedia if they are unfamiliar.
Important tip: If you’ve clipped off the end of wires, make sure they don’t fall on anything that is connected to the power. Clean up before you put powered PCBs on top of those things! If you don’t you might end up damaging things. Most ATX power supplies have a short circuit protection and turn themselves off. You need to unplug the motherboard short (ground/black to green wire in my case, but check to be sure). A video of adapting your PSU can be found here. On the right is my High-Tech ATX PSU conversion deviceTM (also called a wire) that enables the PSU without a motherboard attached.
All added up: It took me about a full day to finish the electronics and test it. Depending on experience this may vary from 0.75 to 3 days.
The entire RepRap is using a maximum of about 50 Watts:
- including my ineffcient ATX PSU (Power supply unit) and
- with all stepper motors on (with hold ’torque’ currents on them).
- With a case fan on
- With the nichrome coil heating a little bit (but it will not be fully on during normal operation).
This kind of power usage is not optimal, but certainly acceptable for now. Better tracking of the X, Y or Z axis positions would allow the hold torque to be minimized. If the steppers would skip this is not a big problem since the software would know about this.
Programming the PICs
I created a programming cable to do ICSP (In Circuit Serial Programming). Now I can use the PicKit 2 from Microchip.com to program everything. I use “pk2cmd” to use this programmer on linux.
Software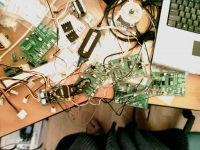
The software was a bit of a hassle. As always, this was not the software’s fault. I am especially good at breaking and then fixing things again. It turns out I had no working GLX support, my nvidia driver didn’t work well under linux. I’ve had it working and fail again over the last few ubuntu distro’s and kernel updates. I think my own fixes or workarounds to problems interfere with things that the Ubuntu team improves. A nice extra is that I’ve got my fancy (and arguably useful) compiz features back (see movie for an impression and to see why windows vista is “soooo 2007”)!
Finally, here’s an image of my progress so far… I’ll keep you posted!
Ken je deze ook?
http://fabathome.org/wiki/index.php?title=Main_Page
Ja die kende ik al langer. Is alleen lang niet zo cool aangezien het self-replication mist. Je moet bijvoorbeeld allerlei laser-cut parts van buitenaf hebben. Vervolgens kan je nog geen voorwerpen maken van dergelijke kwaliteit (zoals machines).
Note to self:
1. Good straight (more durable?) extruder design (without flexible coupling)
http://3dreplicators.com/cgi-bin/cblog/index.php?/archives/345-GM-17-gearmotor-mount-complete.html
2. Wooden Darwin RepStrap: http://bp1.blogger.com/_sVdXgV5IKgE/RyztLb7GsII/AAAAAAAAAQc/NhT56fHATlw/s1600-h/IM000053.JPG
LOL, I need to blog this one: http://xkcd.com/387/
This guy also suggested a materials revolution:
http://en.wikipedia.org/wiki/Alvin_Toffler
Interview:
http://blog.novedge.com/personal_fabrication/index.html
Erik,
Its true that RepRap has created its extruder polyholder part so far but this photo does not show that. These are parts from Bitsfrombites that were soft molded by Ian. Until now RepRaps surface quality is way lower. (On mine…) Only comment though…
Your blog is cool BTW and keep posting its really good to have feedback on experiences! I wish I had time for that too…
Adam